Can pipeline pumps handle varying flow rates and pressures, and if so, how do they adjust?
Pipeline pumps are versatile machines designed to handle varying flow rates and pressures, making them indispensable in fluid transport systems across numerous industries. Whether it's adjusting to fluctuating demands in water supply networks or maintaining consistent pressure in industrial processes, pipeline pumps exhibit robust capabilities in adapting to changing operating conditions.
One of the key mechanisms by which pipeline pumps adjust to varying flow rates and pressures is through speed control. By utilizing variable frequency drives (VFDs) or similar speed control mechanisms, pipeline pumps can modulate the rotational speed of their impellers. This speed modulation directly influences the pump's flow rate, allowing it to match the required flow rates within the system.
During periods of high demand, such as peak water usage hours in municipal water supply networks, pipeline pumps can increase their rotational speed to deliver a higher flow rate. Conversely, during times of reduced demand, the pump can operate at a lower speed to match the decreased flow requirements, thus optimizing energy usage and system efficiency.
Pipeline pumps employ pressure control mechanisms to maintain optimal pressure levels within the system. This is crucial for applications where consistent pressure is paramount, such as in HVAC systems, industrial processes, or firefighting systems. Pressure sensors and control systems monitor the pressure at various points in the pipeline. If the pressure exceeds the desired level, the pump can adjust its speed or impeller position to reduce flow and stabilize the pressure. Conversely, if the pressure drops below the target, the pump can increase speed to boost flow and restore the desired pressure.
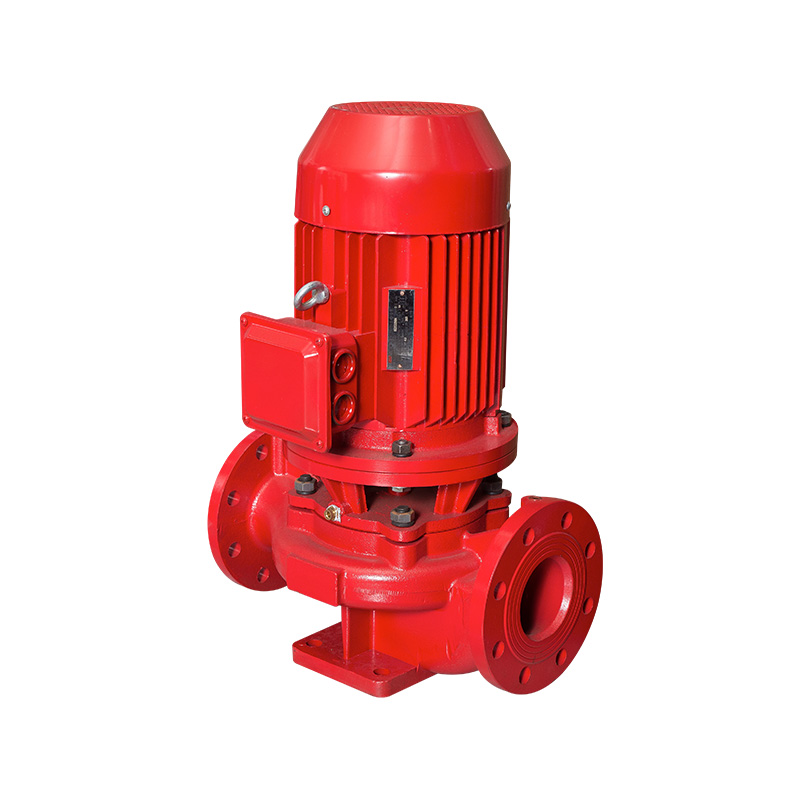
In scenarios where high-pressure delivery is essential, such as in multi-story buildings or industrial settings, multi-stage pipeline pumps are utilized. These pumps feature multiple impellers arranged in series, with each impeller contributing to increasing the pressure of the fluid as it traverses through the pump stages. The number of stages engaged can be adjusted based on the required pressure, allowing for precise pressure control and efficient operation.
Modern pipeline pump systems often integrate advanced automation and control technologies. These systems continuously monitor flow rates, pressures, and other relevant parameters in real-time. Based on the data collected, the automation systems can autonomously adjust pump speed, impeller position, valve settings, and even switch between multiple pumps as needed. This level of automation not only ensures optimal performance but also enhances energy efficiency by dynamically responding to demand variations.