Are there any energy-saving features or technologies incorporated into modern pipeline pumps?
In the realm of fluid handling and wastewater management, the evolution of pump technology has been marked by a relentless pursuit of efficiency and sustainability. As industries and municipalities strive to reduce operational costs and environmental impact, the focus on energy-saving features and technologies in modern pipeline pumps has become paramount.
Variable Frequency Drives (VFDs)
One of the standout innovations driving energy efficiency in modern pipeline pumps is the widespread adoption of Variable Frequency Drives (VFDs). These electronic devices dynamically control the speed of the pump motor by adjusting the frequency of the electrical power supplied. By matching the pump's speed to the actual demand, VFDs eliminate the energy wastage associated with running pumps at full capacity when lower flow rates suffice. This adaptive control not only conserves energy but also extends the lifespan of the pump components by reducing unnecessary wear and tear.
Efficient Motor Design
Integral to the energy-saving prowess of modern pipeline pumps is the utilization of efficient motor designs. High-efficiency motors, compliant with standards such as NEMA Premium or IE3, are engineered to minimize energy losses and maximize power conversion. By employing advanced materials, optimized windings, and precision engineering, these motors deliver superior performance while consuming less energy. The result is a substantial reduction in operational costs over the lifecycle of the pump system.
Optimized Impeller Design
The heart of any pump, the impeller plays a crucial role in determining hydraulic performance and energy efficiency. Modern pipeline pumps feature meticulously engineered impeller designs aimed at reducing hydraulic losses and enhancing overall efficiency. Through computational fluid dynamics (CFD) simulations and iterative design refinements, pump manufacturers achieve optimal impeller geometries that minimize turbulence, improve flow characteristics, and ultimately save energy during operation.
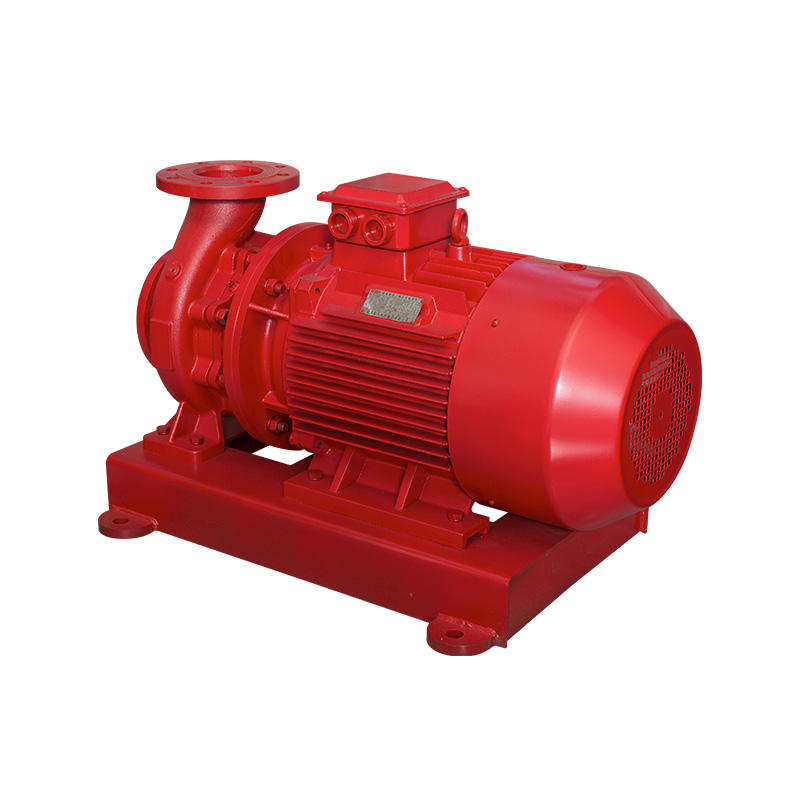
Smart Control Systems
Advancements in automation and control systems have ushered in a new era of intelligence for
pipeline pumps. Smart control systems leverage real-time data and sophisticated algorithms to orchestrate pump operation with unparalleled precision. By analyzing factors such as flow rates, pressure conditions, and system demand, these systems dynamically adjust pump settings to optimize energy usage. Additionally, predictive maintenance capabilities built into smart control systems help prevent downtime and further enhance operational efficiency.
Pump Scheduling and Sequencing
In applications where multiple pumps are deployed, intelligent scheduling and sequencing algorithms play a pivotal role in energy conservation. By coordinating the operation of pumps based on demand forecasts and system requirements, these algorithms ensure that pumps run at optimal speeds and capacities. This proactive approach not only reduces energy consumption but also enhances system reliability and longevity by minimizing stress on pump components.
Energy Monitoring and Reporting
The integration of energy monitoring and reporting features empowers operators and engineers to gain actionable insights into pump performance and energy utilization. Real-time energy monitoring allows for continuous optimization of pump settings, while comprehensive reporting capabilities facilitate data-driven decision-making. By identifying inefficiencies, detecting trends, and implementing corrective measures, stakeholders can fine-tune pump operations for maximum energy savings and operational excellence.